The Stiffel Lamp Company was founded in 1932, in Chicago, Illinois by Ted Stiffel. A talented craftsman, Ted Stiffel had a background in fine arts that gave him a unique ability to design innovative and intelligently crafted lamps, which were also beautiful to behold. Stiffel's dedication to excellence established the company as the industry leader in quality.
During World War II, the company opened up a screw machine department and produced hundreds of thousands of bolts for anti-aircraft guns and other essential components for the war effort. In 1945, after V-J Day, when most government contracts were withdrawn, Stiffel went back to what it did best, making the highest quality metal lamps.
Over the years Stiffel Lamp has contributed a myriad of accomplishments to the lamp industry, including the invention of the patented Stiffel Switch, the pole lamp and unparalleled accomplishments in design. Today that tradition continues with caring and enthusiastic employees, all of whom work towards one common and rare goal – excellence. Proudly all of our products are still made in America, at our 40,000 square foot facility in Linden, NJ. If you take pride in possessing the unusual as well as the finest, then Stiffel should be your choice in lamps. Precise craftsmanship and magnificent design combine to make Stiffel Lamps the world’s finest.
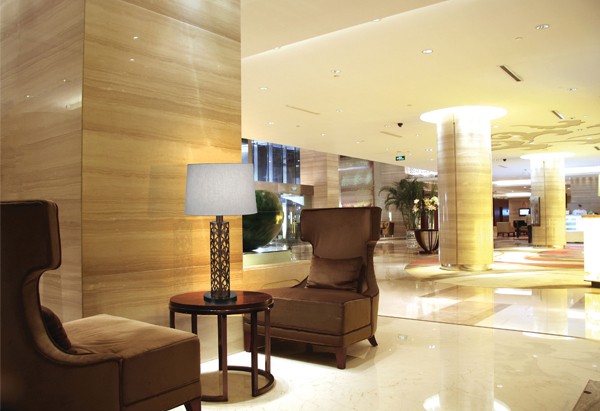
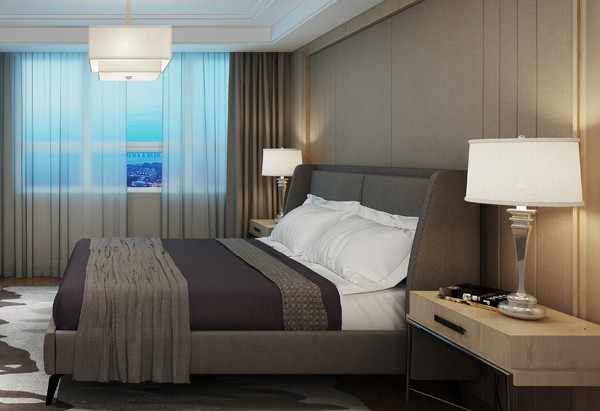
Our Design Process
Many factors combine to make the Stiffel Difference: integrity of design, hand craftsmanship and use of the finest materials. Made in the USA, every Stiffel lamp is an original, created by talented designers and skilled artisans.
A Stiffel lamp has a rare quality that transcends the strictly utilitarian and goes beyond the merely decorative. The purchase of a Stiffel lamp is one of the finest investments you could make for your home.
Of course, there is the obvious beauty and form of the piece, but that is just the beginning. A Stiffel lamp is a work of art. To truly appreciate the beauty of a Stiffel lamp, one must take in each detail and consider the hours of expert craftsmanship that created it: the design, the carving, the finish. A close study reveals the distinguishing value of a Stiffel. It takes dozens of precise steps to achieve this beauty that, in the end, satisfies the tastes and aesthetics of even the most discriminating.
Design
A Stiffel lamp begins with a vision. Each Stiffel lamp evolves from an original design created by our own artists. They take their inspirations from artifacts, architecture or works of art. New designs are scrutinized to insure that they will measure up to Stiffel’s standards. Many of our designs are so unique, they are protected by copyrights.
Mold Making
The artist’s concepts are brought to life by skilled artisans in the mold making process. First, a three-dimensional plaster model is carefully created to serve as a prototype. Every detail is captured and every nuance is faithfully re-created in the model.
From this, a relief-metal mold is made-a finely-crafted reproduction which is machined by hand to insure a flawless fit and appearance. After a cast-iron mold has been produced and thoroughly inspected, it can be released for initial production.
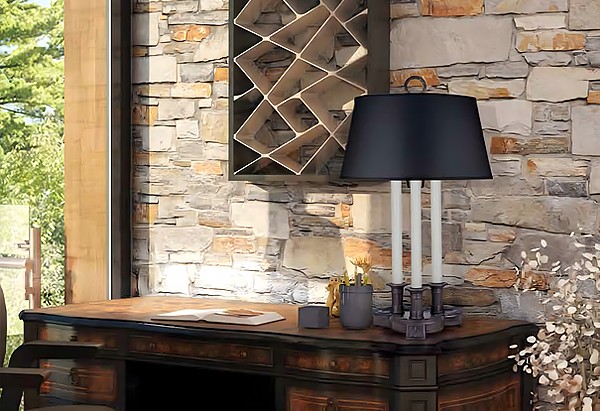
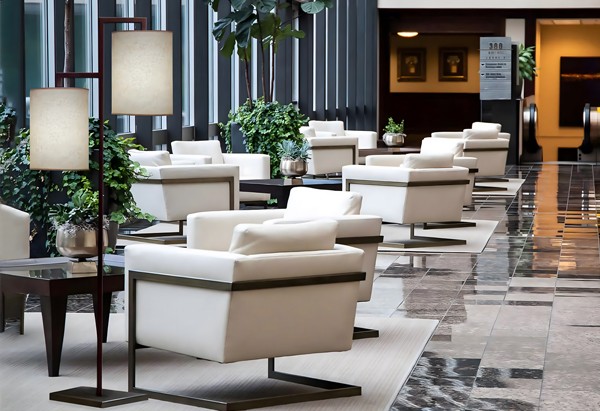
Casting
Hand casting begins where a specially formulated molten metal alloy is poured by hand into the mold. Compare the weight of a Stiffel casting to any other lamp. Many of our competitors add weights to the bottom of their lamps to match the substance that is cast right into a Stiffel. Extraordinary effort is taken to assure that each casting is as close to perfect as possible. Craftsmen-many with more than 20 years of experience-take special pride in their work. When the castings are removed from the mold, the finish is still dull with a rough and grainy texture. Each piece must then be polished repeatedly to achieve the unique Stiffel finish.
Plating
Castings are then taken through a special cleaning and plating process that is uniquely Stiffel. Further cleaning and etching prepares the parts for staininga process that has been developed and refined over half a century. Some special finishes may require as many as twenty separate immersions in special baths and rinses. Traditional designs undergo a treatment where the brass is burnished to an antique patina. First the brass is thoroughly oxidized in special solutions, then hand-buffed to remove some of the antiquing, revealing the warm, natural beauty of the brass.
Final Assembly
Next, castings are assembled and a specially formulated lacquer is applied to preserve and protect the finish. Designs that require it are embellished and enhanced by hand antiquing-another detail that makes that “Stiffel Difference.”
Polishing
Next, the casting seams are smoothed and design details are enhanced through a process called skiving. Many lamp makers consider this step unnecessary, but it is mandatory for a lamp that bears the Stiffel name. Once machined, each part is hand-polished to a radiant shine through a minimum of three polishing operations by skilled artisans.
Wiring & Testing
Each lamp is wired using only the finest of electrical components. A felt bottom is applied to prevent scratching. For a Stiffel lamp to leave the factory, it must pass the industry’s most rigorous standard for quality.
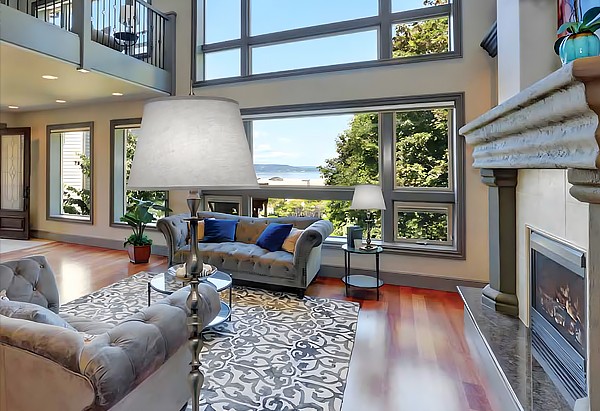
Finishing
The castings are then handfinished in an operation known as “highlighting.” Using a soft-cloth buffing wheel and a special buffing compound-jeweler’s rouge, in some cases-a highly skilled craftsman carefully buffs the casting surface to create a rich, warm finish that is as durable as it is distinctive. Stiffel creates a finish that is untouched in the industry.